在了解玻璃制品的成型方法前,先必须了解玻璃在成型过程中密切相关的性质。
一、与成型有关的玻璃性质
玻璃的成形过程与玻璃的性质有着密切的关系。玻璃的成形性质包括玻璃的黏度、表面张力、结晶性能、热膨胀性、传热性质和热流动性质等。下面就其中几个重要性质作扼要说明。
1 黏度viscosity
粘度,度量流体粘性大小的物理量。又称粘性系数、动力粘度,记为μ。
粘度是衡量流体流动性的指标,表示流体流动的分子间摩擦而产生阻力的大小,有三种表示方法:
动力粘度:面积各为1m2并相距1m的两层流体,以1m/s的速度作相对运动时所产生的内摩擦力。单位:Pa·S(帕.秒)
运动粘度:动力粘度与同温度下该流体密度P之比。单位为m2/s
恩氏粘度:某浓度下,在思氏粘度计中流出200ml液体所需时间与20℃流出同体积蒸馏水所需时间之比。
黏度是玻璃的重要性质之一。玻璃的黏度是温度的函数,并属于非线性的关系,这个关系有利于制品的成形。在玻璃制品的成形过程中,要充分地利用玻璃的黏度和温度的这一关系。
玻璃制品的成形过程可分为两个阶段,即成形阶段和定形阶段。第一个阶段赋予制品以要求的外形(内形),第二阶段是使第一阶段所成的形状固定下来。
通常,玻璃在成形过程第一阶段的粘度为102~103帕··秒,第二阶段的粘度为105.6帕·秒。对于不同系统的玻璃、不同的制品和不同的成形方法,情况不尽相同。
玻璃的黏度与温度的关系和玻璃的化学组成有着密切的和复杂的关系。不同的成形方法要求玻璃具有各不相同的黏度与温度的关系。如浇注成形,要求玻璃粘度小,流动性好,机械化高速成形,则要求“短性”玻璃,而在压制成形时则要求“长性”玻璃。
玻璃成形的工作黏度范围,根据不同的成形方法、制品的大小和质量而不相同。概括地说为102~106Pa.s,一般工业玻璃其上限为5×102Pa.S或103Pa.S,下限通常为4×107Pa.S。小型玻璃制品,其成形的工作黏度范围小;大型制品的工作黏度范围大。
“长性”玻璃的黏度--温度梯度较“短性”玻璃的小,硬化速度较慢,因此其成形的工作黏度范围大,成形过程的持续时间长。在成形过程中如果成形机的结构不可改变,而玻璃制品成形各阶段的持续时间也不能调整,为了适应成形操作的特点与机速的要求,就需要改变玻璃的长短性,即改变玻璃的组成,使之适合。
2 表面张力
表面张力指液体表面任意二相邻部分之间垂直于它们的单位长度分界线相互作用的拉力。
玻璃的表面张力在制品成形过程中有着重要意义。如人工挑料、吹小泡或滴料式供料机,都是借助玻璃的表面张力而形成球形表面的雏形或料滴的。而在拉制玻璃管和玻璃棒时,由于玻璃的表面张力作用才获得正确的圆柱形体。有些玻璃制品成形后还要进行爆口和烧口,也是借助玻璃的表面张力使锋利不齐的边口加热软化变圆滑的。
玻璃的表面张力取决于玻璃的化学组成和温度。在一般情况下,温度升高则玻璃的表面张力降低。熔融玻璃的表面张力比水高3~4倍,与熔融金属相接近,约为0.15~0.35牛/米(150~350达因/厘米).
3 传热性质
玻璃的传热方式为传导和辐射。玻璃制品的成形是热交换过程,特别是第二阶段定形,依赖于玻璃温度的降低。
玻璃是热的不良导体,其传导传热取决于导热系数的大小。玻璃的化学组成和温度决定了导热系数的大小。还应该指出,玻璃在成形过程中的传热是不稳定传热。
辐射传热是玻璃在成形过程中的主要传热方式,特别是在300℃以上时,表现尤为明显。
4 热流动性
从玻璃的黏度性质和传热性质,不难看出,玻璃的成形过程实质上是属于流变学范畴的问题。而玻璃制品的质量在很大程度上取决于成形过程中玻璃的流变状态。这种情况不同于常温的流变学,由于目前对高温玻璃流变学方面的研究水平所限,还没有较完整的理论来指导生产。
二、 玻璃制品的成型方法
由于玻璃的特性:其黏度是随温度变化,无确定的熔点,在成形和定形过程是连续进行的特点,使得玻璃容器有多种的成型方法,是玻璃区别于其它材料的重要特性。
玻璃容器主要的成型方法从成型方法来分有吹制法、压制法、拉制法、浇注法、烧结法等。
从用人工或机械成型来分,又可以区分为人工成型和机械成型。
1 人工成型
在成型机械发明之前,都是由人工成型的。人工成型主要有:人工吹制、自由成型、人工压制、人工拉制等。
⑴ 人工吹制:人工吹制的主要工具是空心的吹杆和衬碳模。
人工吹制的主要工序为:挑料、吹小泡、吹制、加工等。
① 挑料—用一根铁吹管从坩埚的侧口通过旋转吹管来把玻璃蘸出来(图2-1);
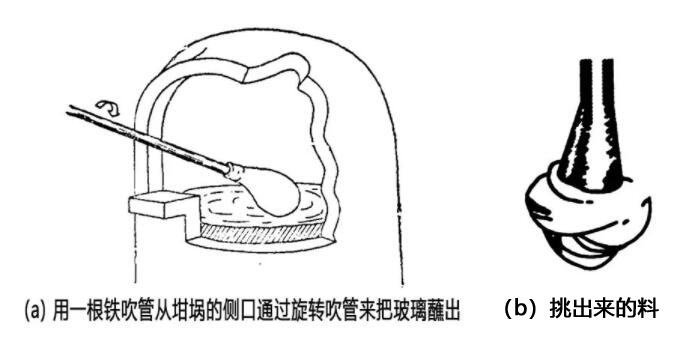
图2-1 人工挑料
②吹小泡—把玻璃从坩埚取出后,在一块滚料板上或滚料碗滚动,使挑的料有一定的形状,平滑的表面。向吹管吹气使玻璃中形成内泡(小泡),如吹制较大的产品,需继续蘸料、滚料,继续吹气,旋转或摆动吹杆,使壁厚均匀,拉长接近模腔的形状(图2-2)。
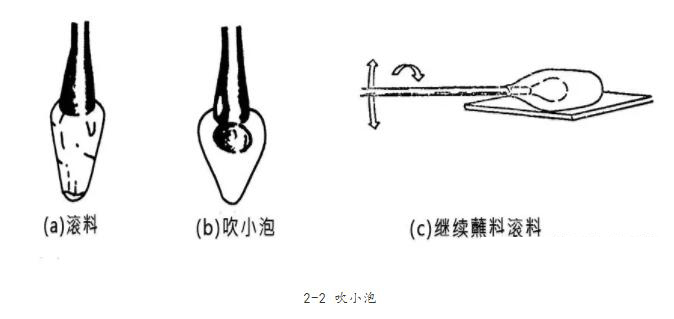
2-2 吹小泡
③ 吹制——将料泡放入村碳模中,入模前,模型用冷水冷却,在不停地转动下,吹气使料泡胀大成为制品。在继续旋转下直至吹成的制品冷却硬化不致变形时取出模外。然后击脱吹管进行修饰(图2-3)。
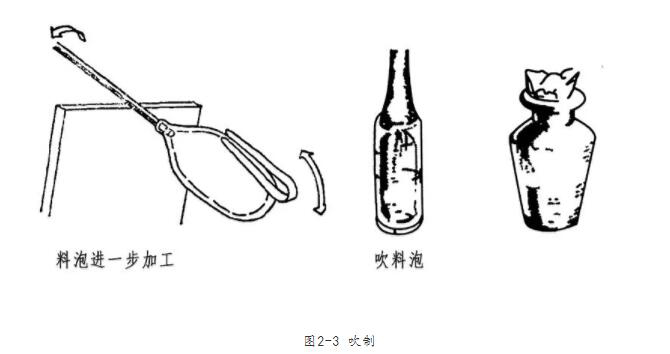
图2-3 吹制
④ 加工——加工或称修饰。在某些情况下,需要在成形时把口部做好。有时,也用特制的夹子夹住制品,然后击脱吹制用的吹管,重新加热制品,用剪刀剪齐口部。在转动下,使制品口部圆滑。有时还需要在制品上粘把,贴花等,最后将制品送去退火(图2-4)。
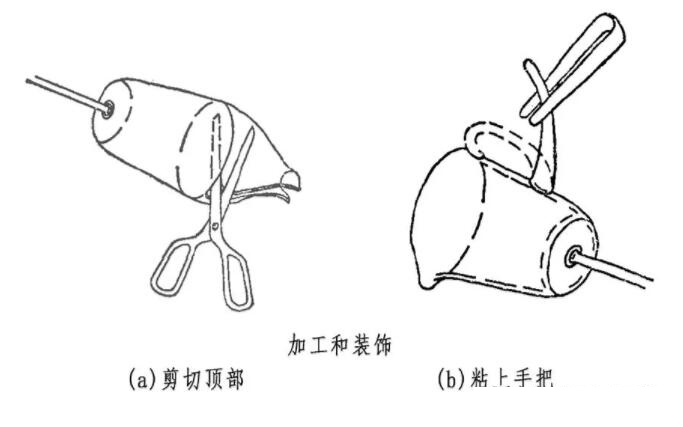
图2-4 加工和装饰
⑵ 自由成型: 不用模子,用一些特制的工具制成玻璃制品,主要用于艺术品的制作。
⑶ 人工拉制:人工拉制主要是指拉制玻璃管(或玻璃棒)的成形方法,它是从吹制法中产生出来的。
主要工序和吹制法相似,即挑料、滚料、做料泡,拉管。在不断地吹气下,以一定的速度拉制成玻璃管。
⑷人工压制:是比较古老的成形方法,实际上是半机械的成形方法。它从挑料,剪料起直至压制,脱模等均借人力操作。它构成形部件主要是模型,冲头和模环,挑起的玻璃料不用滚压,直接在模型上用剪刀剪取一定量使之落入模内,然后放上模环,将模型推至冲头下面,使冲头下压进入模中。这时玻璃液即充满模型,在冲头与模环的空间,形成了制品。冲头应在模中停放一定时间,使制品达到一定硬化程度,不会变形时,抬起冲头,将模型推出并取出制品送往退火。
2 机械成型
在全部实现机械化成形前,玻璃容器还是半机械化成形。当时主要成形空心制品的方法:压一吹法和吹一吹法已经发明。最初,玻璃的挑料,模型的开、关,雏形和制品的转移是人工操作的.其他则由机械进行。
稍后,成形台发展为转台式,转台由人工成电动机操纵。再后除挑料外,模型开、关、雏形转移等也逐步为机械所取代。
⑴ 怎样达到玻璃容器全部机械化生产?
只有解决了玻璃液的机器供料,才能实现全部机械化。
不同的成型机要求的供料方法不同,主要有以下三种:
① 液流供料利用池窑中的玻璃液的流动进行连续供料。一般平板玻璃、压延玻璃、带式吹泡机、玻璃成球机等采用。
② 真空吸料在真空作用下将玻璃液吸出池窑进行供料的方法。用于罗兰式、欧文斯成型机及转吹成型机。它可以是用吸料头吸料(罗兰机、转吹法的吹杯机、吹泡机);也有是用成型机的初型模直接吸料(欧文斯成型机)。
M.J.欧文斯(Owans)和E.D.利贝(Li-bbey) 通过抽除模子中的空气来把玻璃液吸入初型模内。在提出采用旋转式的玻璃液供料盘用来为吸料提供熔化均匀、表层很热的玻璃液的设想后,并经过四台机器多年的实验,终于在1904~1905年获得成功。
③ 滴料供料池窑中的玻璃液经过流料槽,达到所需要的成型温度,供料机制成一定重量和形状的料滴,并经过一定的时间间隔将料滴送入成型机的模具中。
新的有竞争能力的制瓶工艺方法是一种符合制瓶生产要求能够把玻璃液从熔化装置投入初型模的设备,能广泛地应用于各类制瓶机。这种设备就是滴料式供料机。
早期的做法是:从玻璃池窑底部的一个流料孔流出玻璃液带(在1880年后不久),液带绕集在模子中,但这样的玻璃料不密实,温度也不均匀。
1910年以前,早期的滴料式供料机的发展即已开始,在1916年左右获得成功,其概念是通过各种步骤来控制从流料孔流出的玻璃料流成为一个个密实的玻璃料滴。在剪切之前使玻璃料流获得短暂的向下加速,而在剪切后则利用向上的动作把在滴料孔下方的玻璃液流抽回一些。现时所用的料滴式供料机在1923年已经问世,只是近年来有了许多改进。
⑵ 供料机的料滴成型步骤:
① 匀料筒升起,并保持在一定的高度,玻璃液经其下部流入匀料筒中,并从料碗流料孔缓慢流出。此时,冲头加速向下运动,产生向下挤压玻璃液的作用,致使有较多的玻璃液流出流料孔,形成料滴的上部,产生如图“B”所示的形状。
② 冲头停止向下运动,并开始向上行程。此时,在流料孔处的玻璃液变拉长、直径变小,由剪刀剪断而成一个料滴。
③ 冲头加速向上。由于冲头周围的玻璃均粘附在冲头上,因此当冲头向上运动时,能够将玻璃液向上提起一些,甚至将流至流料孔外的玻璃提入流料孔。
④ 冲头匀速向上行至行程的顶端进一步地向上提起玻璃液,并在其顶部位置停止运动一瞬间,待冲头凸轮转过其等径部位,玻璃液在重力作用下缓慢恢复到正常的水平位置。
⑤ 冲头开始它的匀速向下行程。玻璃液首先在重力作用下由流料孔流出,随后在冲头向下挤压的作用下有更多的玻璃液流出,继续如“A”所示的步骤(图2-5)。
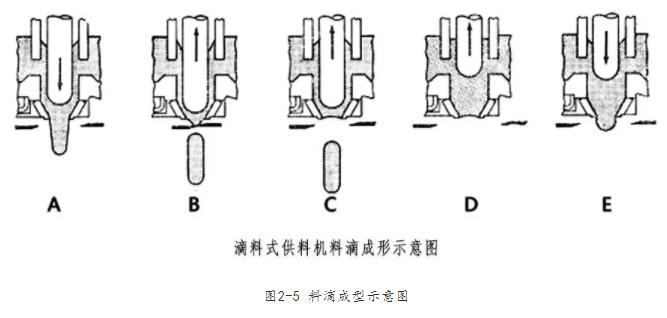
图2-5 料滴成型示意图
⑶ 玻璃容器的机械生产方法
在玻璃制品机械成形的发展过程中,开始是用机器来模仿人工操作。对于吹制来说,则不能像人工吹制一样,采用击脱吹管的办法.因为这样不但不可能有整齐的口部,而且还需要进一步进行加工,即不能在成形机上完整地成形制品。因此,从口部开始成形,便成为机械吹制成形的先决条件。19世纪80~90年代发明的压—吹法和吹一吹法就都先从成形口部来实现机械化成形的。
用于小口瓶生产的吹一吹工艺的基本原理是英国的阿什莱(Ashley)大约在1885年的发明。他发现初塑模必须倒立,才能有大的开孔来接受玻璃料,同时瓶口必须首先成型,并且需用两个模子和一个口钳以及翻倒机构。他曾试图用实心冲头来使玻璃分布合适,但失败了,随后便发展出在初型模中用压缩空气进行“扑吹和倒吹”的作业阶段。
① 吹—吹法生产步骤
吹一吹法的基本原理与人工吹制瓶子相同,先向初型模中吹入压缩空气做成瓶子雏型(称为雏型料泡),再将雏型料泡翻转,交给成形模,向成形模中吹入压缩空气,最后做出瓶子。
吹一吹法的操作工序如下:
a 装料:由料碗落下的料滴装入初型模,为使料滴容易落入初型模,必须使用漏斗。
b 瓶口成形:料滴在初型模中被来自上部的压缩空气压入模内。这时在口模下部为了不使玻璃挤出,冲头自下上升到规定的位置,形成瓶口。
c 吹成雏型料泡:冲头下降,向冲头冲出的凹洞穴自下面吹入压缩空气(称为倒吹气),吹成雏型料泡。这时为了不使玻璃料从初型模底部挤出,用挡板(即初型模底板)盖住模子底部(图2-6)。
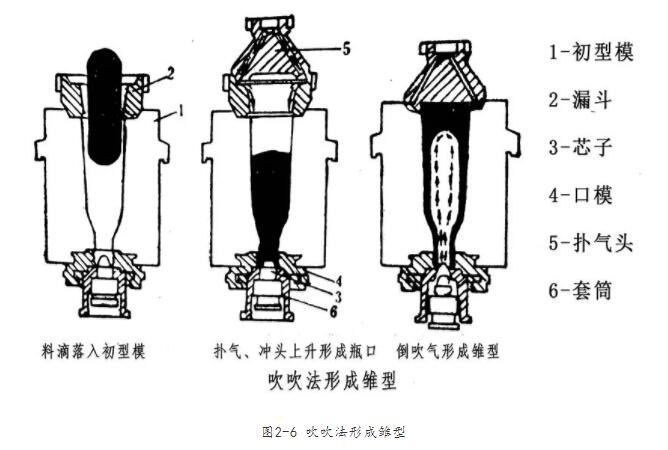
图2-6 吹吹法形成雏型
d 雏型料泡翻转:挡板上升,初型模开放,雏型料泡在被口模夹住的状态下做180°翻转,移送至成形模中,在成形模合上的瞬间,口模放开雏型料泡便完全落入成形模中(图2-7)。
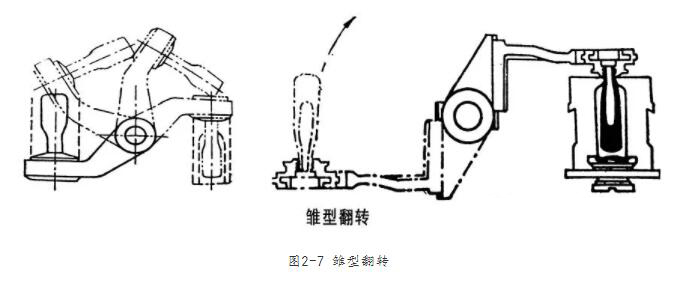
图2-7 雏型翻转
e 重热:与初型模接触的玻璃料泡表面,由于金属模具的吸热而产生硬化层,若立即在成形模中吹制成形则不易得到厚薄均匀、表面光洁的制品。雏型料泡在离开金属初型模后,进入成形模前,使雏型料泡内外玻璃温度分布均匀这一短暂的时间间隔称为“重热”。
f 吹气成形(正吹气):在成形模内,自雏型料泡口部吹入压缩空气(吹气时间可根据需要调整),进行最后的吹气,吹成形状完整的制品。
g 钳移:成形模开放,钳瓶夹具将制品移到固定的风板上。利用拨瓶机构,将风板上冷却的制品按时拨送到送瓶机的输送带上,输送至退火窑前,由推瓶机推入退火窑内进行退火(图2-8)。
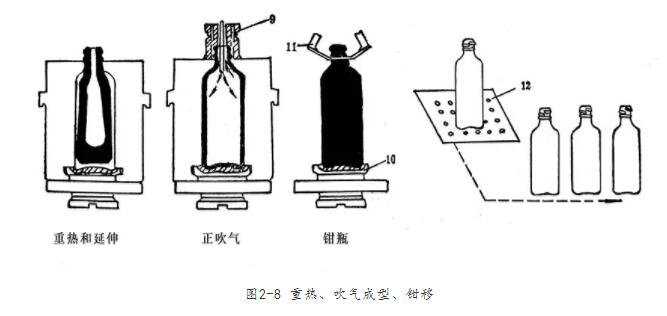
图2-8 重热、吹气成型、钳移
由于在扑气过程,会造成温度不均匀,重热不好,就会形成壁厚不均匀,产生扑气箍。在漫长的制瓶岁月里,人们根据制瓶工艺各自的优缺点,对其进行了一系列改善。瓶口成形采用真空成形,而不用扑气,这样玻璃瓶就不容易出现断腰的现象。并且瓶口部不过冷,它可以改善不良的分布。由此可以减轻瓶重。同时减少了漏斗与闷头的动作,可适当提高机速(图2-9)。
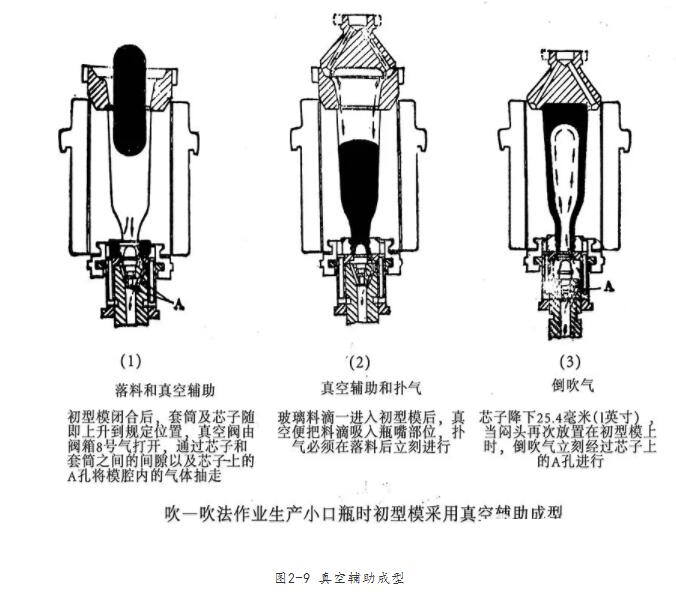
图2-9 真空辅助成型
② LPBB(Light Production Blow&Blow Process)法
捷克斯克劳玻璃机械公司斯克劳玻璃机械公司和德国汉堡国际玻璃技术公司联合开发的吹吹法轻量瓶生产技术(LPBB)。
其基本原理即为应用于瓶罐玻璃工业领域的带真空辅助成型的吹吹法(类似于51工艺或95工艺)。
LPBB®之所以与众不同且更加完美,其原因在于它在基本构件中加入了最新的技术,具体地讲就是由捷克斯克劳玻璃机械公司(SKLOSTROJ)开发的具有专利的真空发生器技术。此真空的产生是由压缩空气冲出射流产生附壁现象,从而产生真空的。这一新型装置为在初型模中的真空辅助成型瓶口及料胚成形的日常使用铺平了道路,从而避免了阻碍该项先进技术广泛应用的各种缺陷。
③ 压—吹法生产步骤
压吹法通常生产大口瓶,它与吹吹法的区别仅在于初型模中雏型的成型方法不同,雏型的内腔是利用冲头压制而成,其过程都相同。
压一吹法的操作工序如下:
a 装料:料碗落下的料滴装入雏型馍内。
b 堵塞:为了不使玻璃料从口模下部挤出,使冲头稍稍上伸,堵住落下的料滴。
c 压成雏型料泡:挡板将锥型模上部盖住,堵住料滴,冲头进一步向上顶压,使玻璃与初型模、挡板、口模紧密贴靠形成瓶口和雏型料泡。
d 重热:冲头下降,雏型模开放,开始雏型料泡的“重热”。
e 翻转:口模夹着雏型料泡做180°翻转传送至成形模内(图10)。
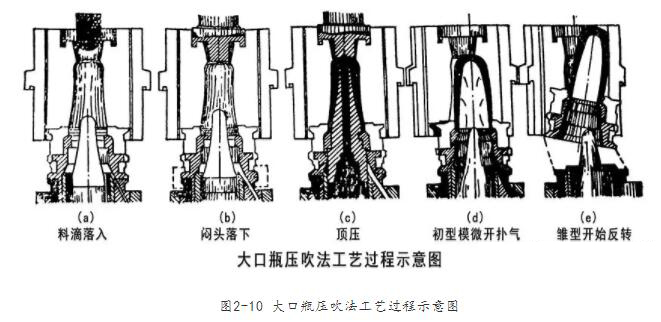
图2-10 大口瓶压吹法工艺过程示意图
f 吹气成形:在成形模内,从雏型料泡口部吹入压缩空气(吹气时间可根据需要调整),进行最后的吹气,吹成完整的制品。
g 钳移:成形模开放,钳瓶夹具将制品移到固定的风板上,利用拨爪将风板上冷却后的制品按时拨到输瓶机的网带上,输送去退火。
原来用压吹法仅用于大口瓶的生产,在70年代由德国海叶公司首次提出小口压吹法并投入生产。
小口压吹的瓶壁均匀度得到大大地提高,因此可以大幅度地减轻瓶重,真正做到了轻量化,并且可以大幅度地提高机速。
小口压吹法在我国近几十年是一个热门的课题。但小口压吹法对工艺技术要求十分严格。它的生产是一个系统的工程,必须认真对待,才能达到满意的效果