使玻璃器皿具有均匀的壁厚可说是成型操作的最理想目标之一。只有压制的玻璃器皿以及玻璃瓶口部的成型是由模子的形状强行决定。而吹制玻璃瓶时的压缩空气或真空则与固定的模子壁面不同。是有伸缩性的。容器的壁厚能否达到均匀则与料泡中的温度及玻璃料的分布有关,看它们是否与成型操作的进行相适应。此在用压缩空气或真空自动成型玻璃容器的操作中必须使这两个参数准确协调一致。首先是料滴的温度均匀以及料滴的形状最为重要,其次就是初型模的容积计算和形状的设计以顺利地达到后来在成型模中制成均匀分布的玻璃料,也就是制品壁分布均匀的要求。
设计初型模时必须充分了解料滴各种尺寸的作用。正确的料滴长度及料滴直径是与容器的重量(料滴重量)有关的重要参数。它们决定着是否能顺利装入模子(进料)。初型模的容积大于所加入的玻璃料的容积。超出的容积部分不应大于50%。它可使料坯的下半部,即靠近初型模底上边的壁厚尽可能厚一些。模子的各个过渡地区都应尽可能十分缓慢地逐渐转变。一方而要做到料滴能顺利地通过模口而不与模子表面产生摩擦。因而料滴的直径要小于模子最狭窄处的直径。另一方面要使料坯内部的温度均衡。如果料坯中的物料量局部有“突变"就会出现温度分布不均匀,造成制品在成型模中吹成后壁厚不均。料坯在吹成时各部分的变化,如扩大、拉长、要求的高度、半径以及形成的曲线等差别是很大的。这些变化都与制品的形状及成型方法(吹一吹法、压-吹法)有关。
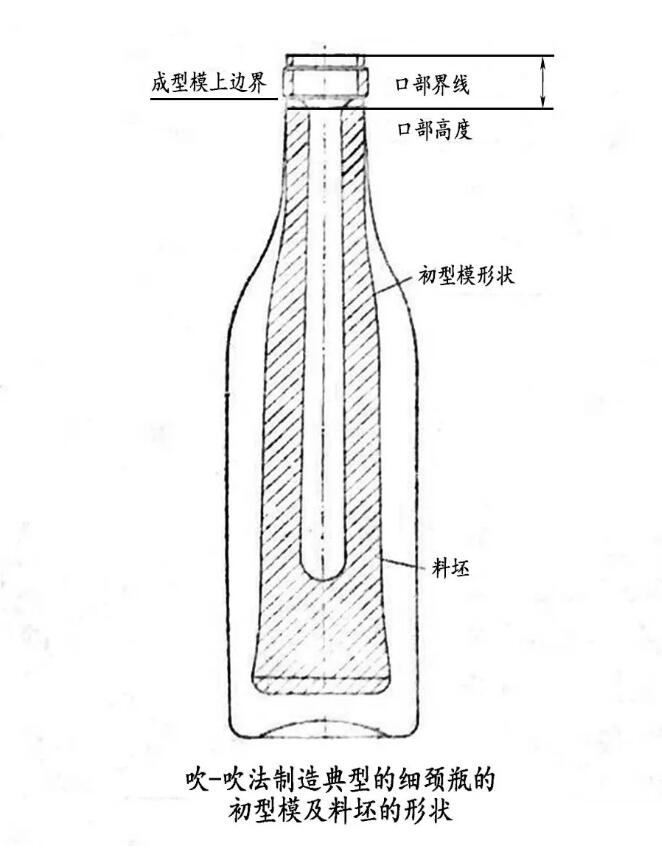
图示出一个典型的细颈标准瓶 (吹一吹法)初型模的剖面 。初型模瓶颈部分的锥形必须足够长才能保证料坯转移时料坯肩部与成型模肩部之间有活动的空隙。特别是对具有明显凸肩的制品在设计初型模时要注意。料坯转移到成型模中时,口模的下边(固着环)必须稍高于成型模口的上边。因为成型模闭合后,料坯还要下降一段才能正确进入成型模中,由于成型模提前闭合,初型模的雏体颈部须长些,料坯才不致被成型模卡住。因此初型模首先总有一个适合于形成瓶颈的锥形部分,而瓶颈与瓶肩过渡处的曲率半径要尽可能大一些。如果取得小时,虽然很接近成型模的形状,但吹成料坯时这部分就很薄而易于冷却,由于终吹时这部分变形不大而结果较别的部分厚。瓶肩部分则要求与成型模稍接近些。料坯的下半部应多含一些玻璃料,使这部分热量充足,保持足够的可塑性,满足终吹时这部分变形最大的要求。料坯底的尺寸及半径应这样选择,使制品在吹成后初型模底的接缝线不要露在瓶底支承面以外。
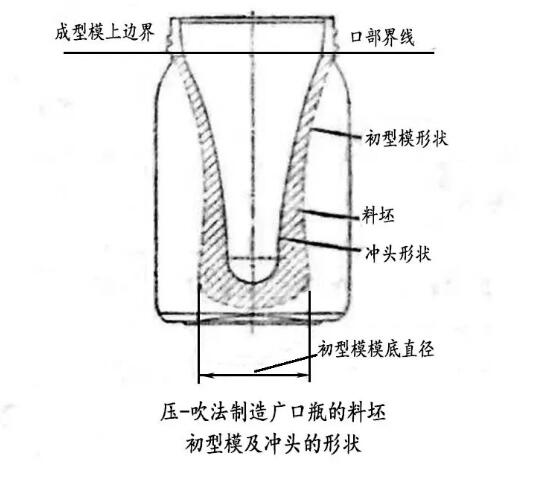
图示出广口制品(压一吹法)的初型模及冲头的形状,如果对开口处的内径没有什么要求时,形成口部内表而的冲头上部(上模)应使这里的玻璃料量尽可能少一些而凝固较快,防止转移到成型模时变形,但也不能使口部太薄,以致压到一半玻璃已凝固,使冲头压不到头,或在冲头的高压下将口部压裂。冲头尖端的半径则由所要求料环底部的厚度(这是关系到瓶底过渡区的壁厚分布的重要参数)以及良好的供料条件(料滴落下)决定。口部线与冲头尖端之间一般由一个锥体连接、设计初型模的形状应注意料环的壁厚是朝着底部方向不断增大,即初型模要约从中部起开始时锥体逐渐扩大然后又缩小。
压一吹法一个极大的优点是冲头及初型模给料坯强制规定了内外表面的形状,使其壁厚分布均匀,从而给制成品的均匀壁厚打下良好的基础。这也是目前用压一吹法制造细颈瓶日益扩广的原因。它能使制品壁厚均匀分布。这也是目前制造薄壁容器的关键问题。
①瓶壁薄
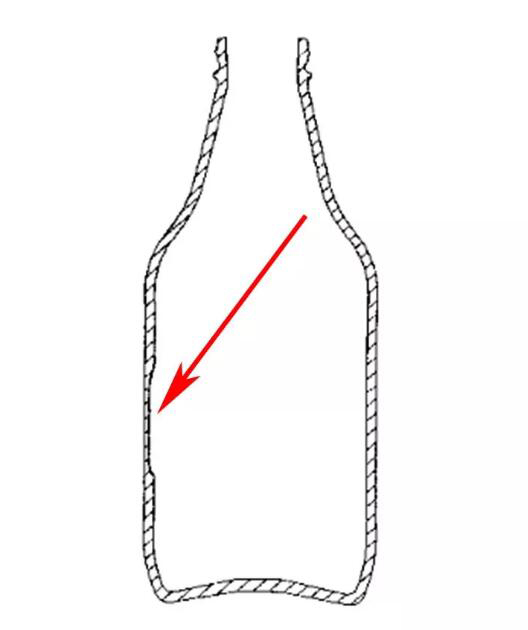
成型机的调节和操作都要本着与初型模的形状相适应这一基本观念。即使玻璃料在初型模中快速成型,应尽可能保持它的含热量并将整个膜腔均匀而充分填充。玻璃料部分提前凝固或温度太高都会导致壁厚分布不均匀。图示出一个容器壁上有太薄的部分。缺陷生成的原因可能是模子冷却不均匀,也可能是初型模与玻璃的接触时间不够长,离开模子时玻璃料太热 在重力作用下向下流淌。压一吹法中冲头的冷却也是十分重要的料坯的重热时间太长,终吹开始时间推迟,也可能与上述缺陷产生有关。
②瓶肩薄
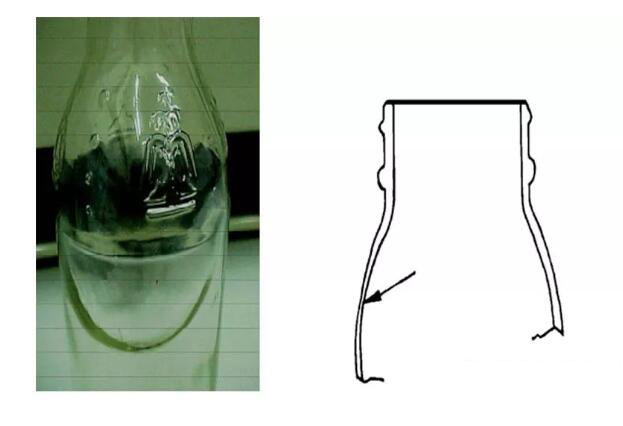
产生的原因常是由于料坯的相应部分没有正确冷却或润滑而温度过高,或终吹开始时间太晚而使料坯过多地伸长。
③瓶底厚、薄或偏底
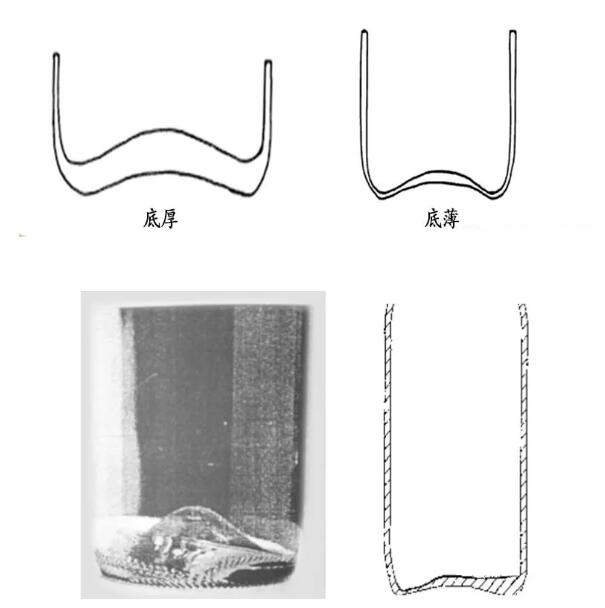
图示出一种底厚的现象,虽然这只是一种外观缺陷,但会造成容器的其他部分壁厚不足,原因也可能是料坯重热时间太长或吹开始太晚,玻璃在重力的作用下流向瓶底。重热时间及终吹时间的规定本来就是为了使料坯的底部玻璃多一些,现在当然是过分。初型模底或成型模底的温度不够高也可能造成料坯的厚底展开困难,在机器的调试过程中有时也出现瓶底过薄的情况。与上述对比正好是走上了另一个极端,即料坯的重热时间太短,终吹开始的时间过早或底模温度太高。有的容器器底部一边薄、一边厚即底部歪斜,就应当检查初型模或成型模的温度否均匀,口模的夹具位置是否恰当,即料坯进入成型模中时是杏垂直向下落。有时也会发现吹入成型模中的冷却空气流的方向没有控制好而使料坯在成型模闭合时向一侧歪斜。成型模底部排气不均匀也常造成斜底。