玻璃模具等离子焊自动生产线用于完成玻璃模具的自动上料、自动预热、自动转运、自动下料等任务,实现玻璃模具等离子焊接过程的自动化。
本章针对玻璃模具的结构特点,对多品种、小批量玻璃模具的等离子焊自动生产线的系统组成进行了规划,并对系统各部分的总体方案进行设计,主要包括自动上料系统、高效节能加热炉、转运机构、焊接下料机构以及整体控制系统等方案设计。
2.1玻璃模具
2.1.1型腔结构特点
玻璃模具种类繁多,可根据不同的应用要求选择不同的形状和尺寸,具有极广的选择范围。本文主要是以类半圆形玻璃模具为研究对象,设计一套玻璃模具等离子焊接自动生产线,首先需要分析等离子焊接的目标对象的结构特征,即玻璃模具的型腔结构特征。玻璃瓶罐模具的内部型腔结构几乎各不相同,成模的内型腔结构与用其成模所生产出的玻璃瓶罐的外形结构是完全相同的,而初模的内型腔结构具有多样性、无规律性,但其内型腔结构大小一定小于对应成模的内型腔结构;而玻璃瓶罐模具的外部轮廓结构特征大致相同。玻璃模具H维图示意图如图2-l(a)所示,其主要外形尺寸如图2-1(b)所示。
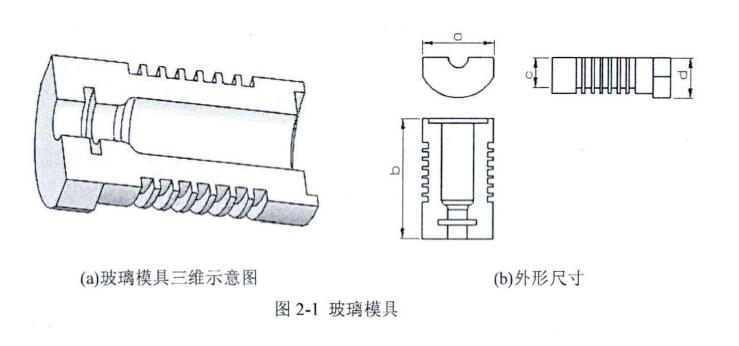
2.1.2玻璃模具尺寸特征
由于玻璃瓶罐大小不一,其长度和宽度尺寸也具有多样化。因此对应的巧璃模具也有不同的尺寸-本文所针对的玻璃模具主要尺寸系列如表2-1所示。


表2-1玻璃瓶罐模具的尺寸系列
由上可知玻璃模具的尺寸跨度较大、外形复杂,转运和焊接难度都会很大,而对于本文所设计的生产线要完全适用于满足具有W上尺寸的玻璃模具,可知该生产线的设计的存在一定的难度。
2.2功能需求分析
结合合作企业所提要求和相关行业标准,玻璃模具等离子焊接自动生产线系统应满足W下功能需求和技术指标:
(1)设计用途;该生产线主要用于多品种、小批量的玻璃模具工件的自动上料、自动预热、自动转运、等离子焊接及自动下料。
(2)巧适用工件尺寸:适用于该生产线的玻璃模具尺寸如表2-1所示,设计时需要确保最大外形尺寸的玻璃模具可良好的适巧于生产线,避免大工件在焊接和预热过程中发生卡顿现象。
(3)生产线生产效率:在确保模具预热温度的前提下,满足等离子焊接效率约为1件/min。
(4)巧接工艺要求:对玻璃模具合缝面和合缝线处进行等离子焊接后,使焊层厚度达到0.7-0.9mm,宽度达2.8-3.0mm,焊层的硬度达到280-300HBW。
(5)可靠性和安全性:生产线的机械结构和控制系统具有较髙的稳定性和可靠性:生产线具有检测巧报功能,当生产线运行出现状况时,检测系统可及时检测出异常情况并发出巧报信号。
2.3系统组成
玻璃模具等离子焊自动生产线由上料运送机构、上料气缸推动装置、液压缸推动装置、上料拨动装置、转运小车、送料小车、控制系统、传感器等组成I按其功能可分为自动上料系统、外循环系统、商效节能加热炉等,其中外循环系统主要包括上料机构、循环转运机构、焊接下料机构.该生产线系统结构组成框图如图2-2所示。
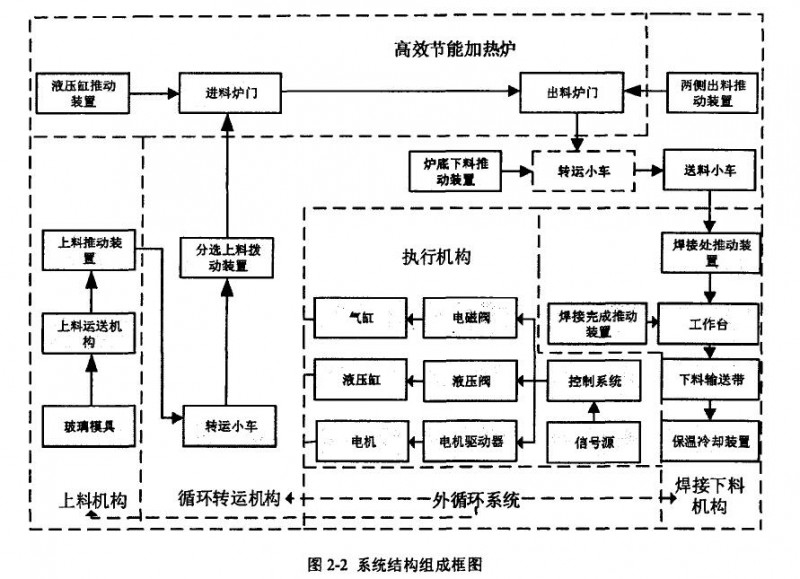
玻璃模具等离子焊接自动生产线的工作过程为:将待预热玻璃模具放置在上料运送装置上,由输送链条链板带动工件以固定的姿态向上运行,可根据玻璃模具的大小切换不同的传感器,以保证工件到位的准确性;待传感器检测到到位信号,上料气缸动作推动工件至转运小车中的托盘上进行上料;托盘和工件随转运小车运动至进料炉口处,分选上料拔动气缸动作,推动托盘和工件至进料炉口处,转运小车运动至出料日处;炉口升起到位后,液圧缸动作推动托盘和工件向前运动,工件到达出料炉口处,炉口下降至指定位置后,侧面气缸推动工件和托盘至转运小车上,炉底下料气缸动作推动工件至送料小车上,同时托盘在转运小车的带动下回到初始位置进行重新上料,至此系统完成一次循环上料过程。预热完成的工件通过送料小车运送至工作台进行等离子招接;控制系统控制通过检测外部信号控制整条生产线的气缸、液压缸、电机动作;炉内温度检测系统中实时检测炉内温度,在温度达到要求时进行玻璃模具的出料动作。玻璃模具等离子焊自动生产线将周期性的对多品种、小批量的玻璃模具进行自动上料、自动预热、自动转运、自动送料、等离子焊接以及自动下料。
玻璃模具等离子焊接自动生产线的工作流程如图2-3所示。
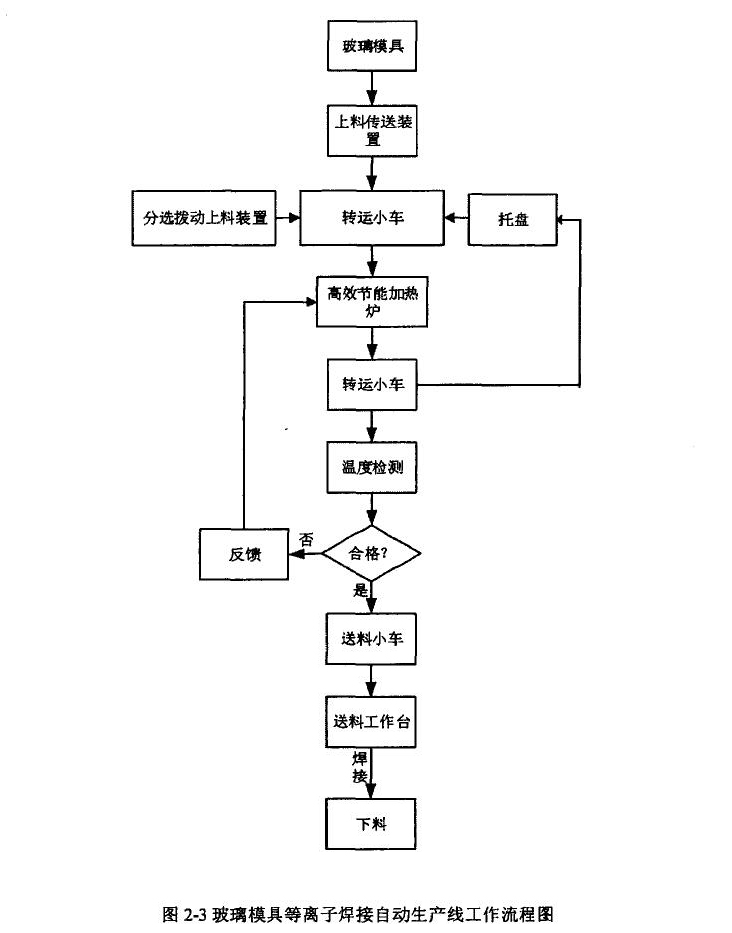
2.4系统总体方案设计
玻璃模具等离子焊接自动生产线的总体方案设计可分为玻璃模具等离子焊接自动生产线外循环系统总体方案设计和高效节能加热炉总体方案设计。其中玻璃模具等离子焊接自动生产线外循环系统总体方案设计包括:自动上料系统总体方案设计、循环转运机构总体方案设计、巧接下料机构总体方案设计以及控制系统总体方案设计。
(1)自动上料系统总体方案设计
自动上料系绕是玻璃模具等离子焊接自动生产线外循环系统的基础,主要包括上料链板、上料链条、上料推动装置、机架等零部件。其中上料链板和链条用于支撑并运送待预热焊接的玻璃模具至指定上料区域;上料推动装置用于将等待预热的工件推送至转运小车进行上料;机架则是安装链条板、链条、电化、上料推动装置等附件的基体。
由于玻璃模具外形复杂导致工件之间容易发生相互干涉的现象,且为保证供料速度能满足系统的要求,上料时应合理的布置工件相互之间的距离。针对玻璃模具类半圆形的外形W及多品种小批量特点,需设计通用性上料推动装置。为解决工件在上料至转运托盘中的准确定位问题,在上料曰至转运小车之间设计导向和过渡装畳以保证工件能准确上料至转运小车上。另外,为满足不同大小玻璃模具准确上料的要求,应设计接近开关和光电传感器两者相互切换装置,确保模具能准确停在指定位置。
(2)循环转运机构总体方案设计
循环转运机构可分为分选上料拨动装置、转运小车、侧面推动装置以及炉底下料推动装置。为满足多品种、小批量玻璃模具通用性上料W及预热要求,特设计通用托盘来满足不同大小的玻璃模具的转运和预热。为满足工件的循环上料,特设计转运小车配合转运托盘进行循环工作。当托盘随转运小车在电机和链条的带动下运动至上料口,上料气缸推动待预热工件至转运小车的托盘上。然后转运小车随托盘和工件运动至进料炉口处,托盘和工件一起进入炉内,此时转运小车运动至出料炉口处来转接出料口托盘,在炉底下稱气缸的作用下预热后的工件和托盘分离,随后转运小车随托盘运动至上料口进行重新上料。为提高预热效率并节省空间特设计了双箱体高效节能智能化加热炉,此时要对转运至小车上的工件进行分别上料,需设计分选上稱拨动装置,从而使工件分别进入1、2炉箱内进行预热。此分选上料拨动装置在炉底相对狭小的空间内要准确满足上料要求,且不能与1、2号升降炉门干涉。此外由于炉口处温度较髙,设计时应尽量远离炉门,避免温度较高。当工件达到预热温度,出料炉口下降,为完成出料动作,需设计侧面推动装置,推动工件和托盘至转运小车上。炉底下料推动装置用于分离预热后的高温工件和托盘,设计时需充分考虑空间和高温等条件。
(3)焊接下料机构总体方案设计
焊接下料机构是针对预热后的高温玻璃模具,完成模具工件的送料、等离子焊接、下料运输以及集中缓慢冷却处理。具体可分为送料小车、焊接前推动装置、工作台以及下料输送装置。炉底下料推动装置推动完成预热后的工件进行下料时,巧设计送料小车运送预热后工件至各个工作台进行等离子焊接,要求送料小车运行过程中速度适中、安全可靠、定位准确。当送料小车运动至指定工位时,焊接前推动装置推动工件至工作台进行等离子挥接。设计导向板以及过渡板以保证工件上料的平稳性,同时为保证工作台上料的安全性,特设计气缸夹持机构,保证工件在可控的情况下平稳运行。根据玻璃模具复杂的外形特点以及模具进行等离子焊接位置的不确定化设计4个可旋转式焊接工作台。该工作台包括焊接完成下料装置和下料导轨等可对完成焊接后的工件进行下料。工件完成焊接后,需对工件进行集中保温处理.设计下料输送装置,输送工件至保温箱内。
(4)商效节能加热炉总体方案设计
高效节能加热炉是玻璃模具等离子焊接自动生产线的核也组成部分,其主要包括:液压缸推动装置、炉口升降机构、双箱炉体以及炉内导轨等。该加热炉特点是高效、节能且满足品种、小批量的玻璃模具的预热温度为750℃左右高温预热要求。在不提高预热温度并节约成本的条件下,设计双箱体高效节能加热炉,极大的提高预热效率。可根据实际生产情况选择1、2号炉单独王作或者同时工作,满足自动生产线的柔性化生产要求。设计液压缸推动装置,为托盘和工件在炉内运动提供充足驱动力,但要充分保证液皮缸推动装置的稳定性。设计炉内导轨配合托盘完成玻璃模具在炉内的循环预热过程。为减少炉门开关时造成热量的损失,特设计炉体底部自动化升降炉口,用于自动化进出料。
(5)控制系统总体方案设计
控制系统是玻璃模具等离子焊接自动生产线得以正常运行的保证。在对国内外生产线采用的不同类型的控制系统进行深入研究的基础上,确定该自动生产线控制系统采用PLC作为整个系统的控制核也,以触摸屏作为人机交互界面。为确保玻璃模具上料的稳定性和准确性,需对上料输送装置、上稱推动装置的控制进行设计;为确保系统周期性托盘循环上料,需对转运机构的运动控制进行设计;为确保商效节能加热炉满足多品种、小批量复杂外形的玻璃模具的自动化高温预热要求。需对加热炉的控制进行设计:为确保预热后的玻璃模具完成等离子焊接工作,需对焊接下料机构的控制进行设计。此外,为确保本系统能够安全可靠的运行,控制系统应不断监测系统的运行状态。当系统发生故障时,警示工作人员排除故障并恢复系统运行。
2.5本章小结
本章首先介绍了玻璃模具的结构特点,并对其外形尺寸特点进行了详细说明;然后针对其特点-对玻璃模具等离子焊接自动生产线的系统组成进行了规划,将系统划分为自动上料系统、转运机构、商效节能加热炉、焊接下料机构和控制系统等部分,并对系统各部分之间协调工作的过程进行了详细阐述;最后对系统各部分的总体方案进行了设计,分析了自动上料系统、控制系统、转运机构、高效节能加热炉、焊接下料机构设计时的关键问题,明确了各部分的设计要求,细化了各部分所要完成的设计任务。